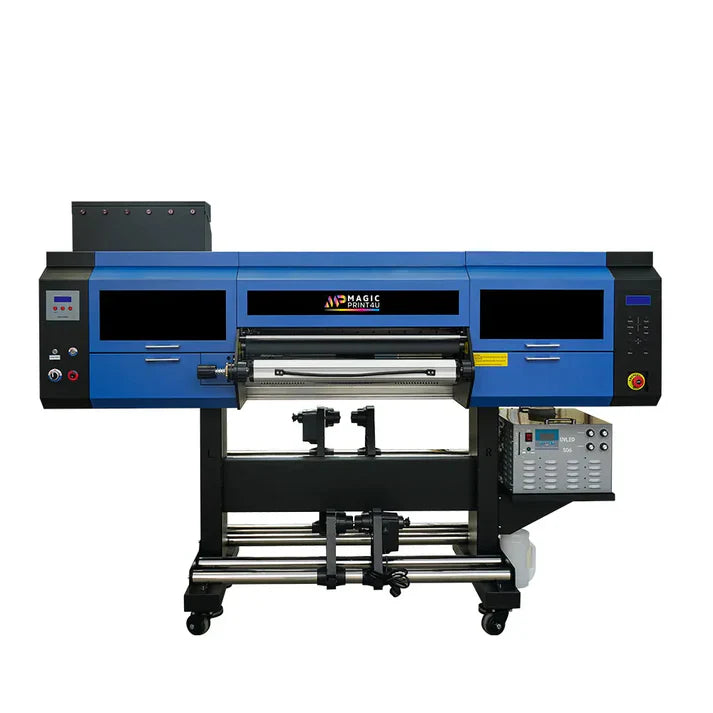
Things to Consider When Purchasing a UV DTF Printer
Investing in a UV DTF (Direct-to-Film) printer is a strategic decision for any business or creative professional looking to produce vibrant, durable prints on a wide variety of substrates. Below is a comprehensive guide to help you choose the ideal UV DTF printer for your needs.
UV-Curing Technology
How It Works
UV DTF printers employ UV-curable inks that harden when exposed to ultraviolet light. As the ink is laid down on the special film, an integrated UV lamp immediately activates, triggering a photochemical reaction that polymerizes the ink.
Key Advantages
- Instant Drying: Prints come off the machine ready for transfer, eliminating smudging or smearing.
- Superior Adhesion: UV-cured ink forms a strong bond with textured, irregular, or non-porous surfaces.
- Enhanced Durability: Cured prints resist scratching, fading, and exposure to moisture or chemicals.
Print Quality and Resolution
Resolution (DPI)
Look for models that support at least 600 × 1200 dpi; higher resolutions (up to 2400 dpi) yield finer detail and smoother gradients.
Color Gamut and Ink Configuration
- CMYK + White: A dedicated white ink channel ensures true opacity on dark or transparent materials.
- Expanded Gamut Options: Some printers offer additional channels (e.g., Light Cyan, Light Magenta) for more accurate color reproduction.
Integrated Printing and Lamination
An all-in-one system prints and laminates in a single pass, saving time and ensuring uniform results without bubbles or wrinkles.
Ink Management and Circulation
Automatic ink monitoring and refill systems prevent low-ink interruptions, while white-ink stirrers keep pigment evenly dispersed to avoid clogs.
Media Handling and Take-Up
A reliable front take-up mechanism smoothly rolls finished prints. Check maximum roll diameter, tension control, and speed settings for uninterrupted production.
Safety and Collision Protection
Anti-collision sensors detect obstructions and immediately halt operation. UV-protected housings and interlock mechanisms shield users from harmful exposure.
Roller and Contact Design
High-quality laminated rubber rollers adapt to surface variations, ensuring even pressure and flawless contact. Look for replaceable sleeves and adjustable pressure settings.
Software and RIP Support
User-friendly control software and a dedicated RIP (Raster Image Processor) provide color profiling, job queue management, and nesting/tiling to optimize material use.
Total Cost of Ownership
Beyond the printer’s sticker price, account for installation, training, consumables (ink, film, maintenance kits), and spare-parts availability to calculate long-term expenses.
Application Flexibility
Verify substrate compatibility—metals, glass, plastics, wood, textiles, leather—and ensure the printer’s maximum width and length meet your production requirements.
Featured Model: MP UV-DTF Printer 2.4
One standout option that ticks almost every box is the MP UV-DTF Printer 2.4. Key features include:
- UV-Curing Technology for instant drying
- Integrated Printing and Lamination in a single pass
- Automatic Ink Supply and white-ink circulation
- Anti-Collision System and efficient front take-up
- Laminated Rubber Rollers for flawless contact
Final Recommendations
- Request Samples or Demonstrations: Test-print your typical substrates to evaluate adhesion, color fidelity, and durability firsthand.
- Check Vendor Support: Ensure the manufacturer offers comprehensive technical support, on-site service, and training.
- Assess Scalability: Choose a model that can grow with your business—modular upgrades, additional heads, or larger formats.